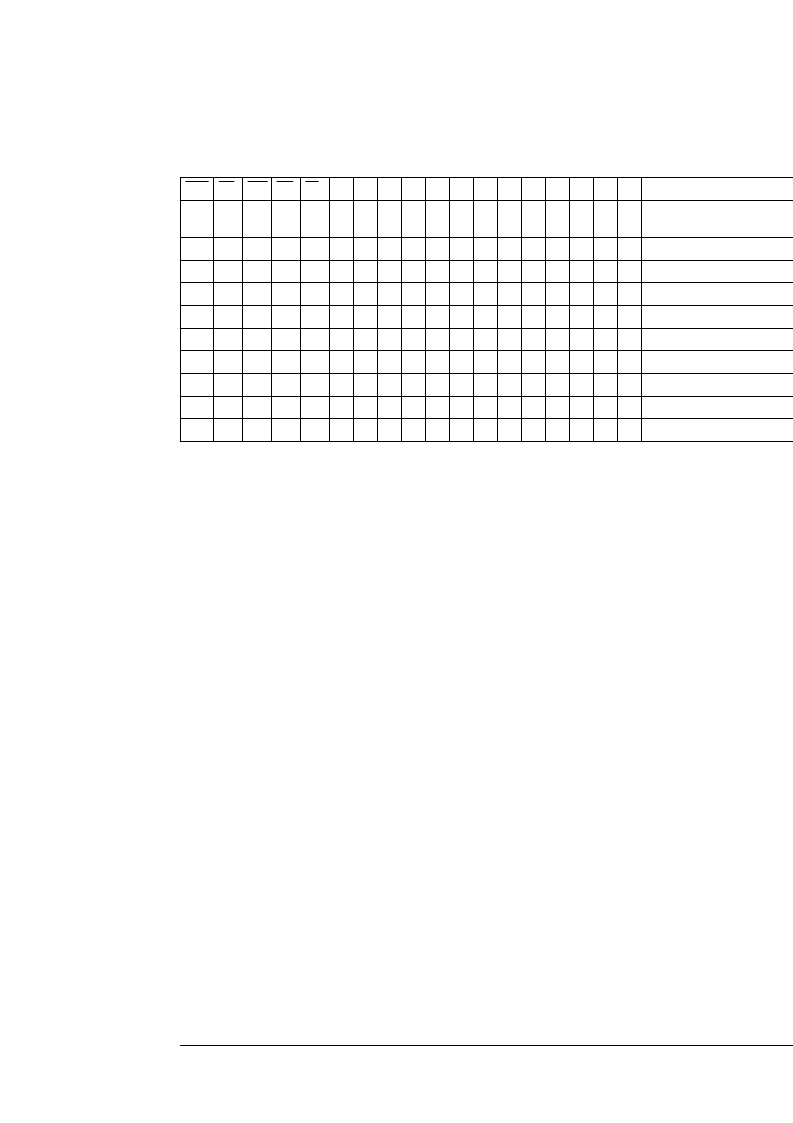
2000 In
fi
neon Technologies Corp.
Optoelectronics Division
San Jose, CA
www.in
fi
neon.com/opto
1-888-In
fi
neon (1-888-463-4636)
OSRAM Opto Semiconductors GmbH & Co. OHG
Regensburg, Germany
www.osram-os.com
+49-941-202-7178
HDSP2110S/1S/2S/3S/4S/5S
12
March 24, 2000-13
Figure 16. Displaying User Defined Character Example
Load character “A” into UDC-5 and then display it in digit 2
Logic levels: 0=Low, 1=High, X=Don‘t care
Electrical and Mechanical Considerations
Voltage Transient Suppression
For best results power the display and the components that
interface with the display to avoid logic inputs higher than
V
CC
.
Additionally, the LEDs may cause transients in the power sup-
ply line while they change display states. The common practice
is to place a parallel combination of a .01
μ
F and a 22
μ
F capac-
itor between
V
CC
and GND for all display packages.
ESD Protection
The input protection structure of the HDSP211XS provides sig-
nificant protection against ESD damage. It is capable of with-
standing discharges greater than 2.0 kV. Take all the standard
precautions, normal for CMOS components. These include
properly grounding personnel, tools, tables, and transport carri-
ers that come in contact with unshielded parts. If these condi-
tions are not, or cannot be met, keep the leads of the device
shorted together or the parts in antistatic packaging.
Soldering
Considerations
The HDSP211XS can be hand soldered with SN63 solder using
a grounded iron set to 260
°
C.
Wave soldering is also possible following these conditions:
Preheat that does not exceed 93
°
C on the solder side of the PC
board or a package surface temperature of 85
°
C. Water soluble
organic acid flux (except carboxylic acid) or rosin-based RMA
flux without alcohol can be used.
Direct contact with alcohol or alcohol vapor will cause degrada-
tion of the package.
Wave temperature of 245
°
C
±
5
°
C with a dwell between 1.5
sec. to 3.0 sec. Exposure to the wave should not exceed
temperatures above 260°C for five seconds at 0.063" below
the seating plane. The packages should not be immersed in
the wave.
RST CE
WR RD
FL
A4 A3 A2 A1 A0 D7 D6 D5 D4 D3 D2 D1 D0 Operation
Display
0
X
1
1
1
X
X
X
X
X
X
X
X
X
X
X
X
X
Reset. No Read/Write
Within 3 Clock Cycles
All Blank
1
0
0
1
1
0
0
X
X
X
X
X
X
X
0
1
0
1
Select UDC-5
All Blank
1
0
0
1
1
0
1
0
0
0
X
X
X
0
1
1
1
0
Write into Row 1 of UDC-5
All Blank
1
0
0
1
1
0
1
0
0
1
X
X
X
1
0
0
0
1
Write into Row 2 of UDC-5
All Blank
1
0
0
1
1
0
1
0
1
0
X
X
X
1
0
0
0
1
Write into Row 3 of UDC-5
All Blank
1
0
0
1
1
0
1
0
1
1
X
X
X
1
1
1
1
1
Write into Row 4 of UDC-5
All Blank
1
0
0
1
1
0
1
1
0
0
X
X
X
1
0
0
0
1
Write into Row 5 of UDC-5
All Blank
1
0
0
1
1
0
1
1
0
1
X
X
X
1
0
0
0
1
Write into Row 6 of UDC-5
All Blank
1
0
0
1
1
0
1
1
1
0
X
X
X
1
0
0
0
1
Write into Row 7 of UDC-5
All Blank
1
0
0
1
1
1
1
0
1
0
1
X
X
X
0
1
0
1
Write UDC-5 into Digit 2
(Digit 2) A
Post Solder Cleaning Procedures
The least offensive cleaning solution is hot D.I. water (60°C) for
less than 15 minutes. Addition of mild saponifiers is accept-
able. Do not use commercial dishwasher detergents.
For faster cleaning, solvents may be used. Exercise care in
choosing solvents as some may chemically attack the nylon
package. Maximum exposure should not exceed two minutes
at elevated temperatures. Acceptable solvents are TF (trichorot-
rifluorethane), TA, 111 Trichloroethane, and unheated ace-
tone.
(1)
Note:
1)
Acceptable commercial solvents are: Basic TF, Arklone, P.
Genesolv, D. Genesolv DA, Blaco-Tron TF, Blaco-Tron TA, and
Freon TA.
Unacceptable solvents contain alcohol, methanol, methylene
chloride, ethanol, TP35, TCM, TMC, TMS+, TE, or TES.
Since many commercial mixtures exist, contact a solvent
vendor for chemical composition information. Some major
solvent manufacturers are: Allied Chemical Corporation,
Specialty Chemical Division, Morristown, NJ; Baron-
Blakeslee, Chicago, IL; Dow Chemical, Midland, MI; E.I.
DuPont de Nemours & Co., Wilmington, DE.
For further information refer to Appnotes 18 and 19 at
www.infineon.com/opto.
An alternative to soldering and cleaning the display modules is
to use sockets. Naturally, 28 pin DIP sockets .600" wide with
.100" centers work well for single displays. Multiple display
assemblies are best handled by longer SIP sockets or DIP sock-
ets when available for uniform package alignment. Socket man-
ufacturers are Aries Electronics, Inc., Frenchtown, NJ; Garry
Manufacturing, New Brunswick, NJ; Robinson-Nugent, New
Albany, IN; and Samtec Electronic Hardward, New Albany, IN.
For further information refer to Appnote 22 at www.infin-
eon.com/opto.