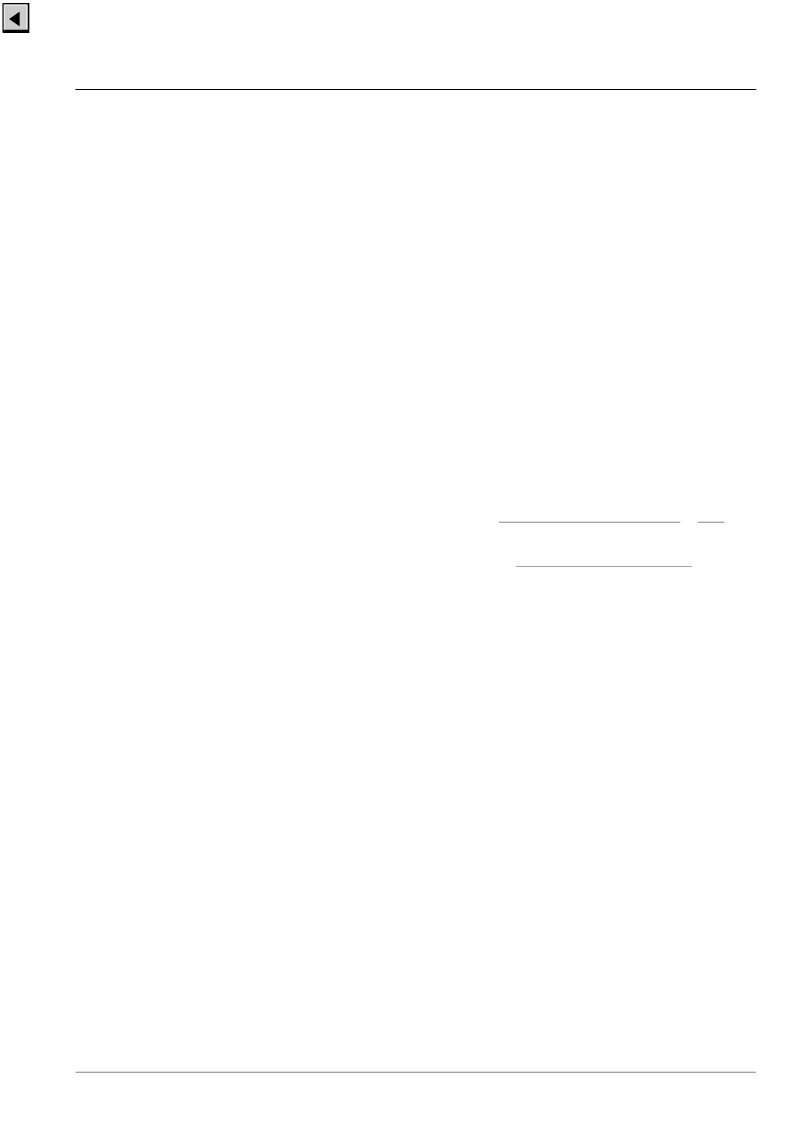
HAL800
Micronas
9
2.3. Calibration Procedure
2.3.1. General Procedure
For calibration in the system environment, the applica-
tion kit from Micronas is recommended. It contains the
hardware for the generation of the serial telegram for
programming and the corresponding software for the
input of the register values.
In this section, programming of the sensor with this
programming tool is explained. Please refer to
Section 5. on page 19
for information about program-
ming without this tool.
For the individual calibration of each sensor in the cus-
tomer application, a two point adjustment is recom-
mended (see
Fig. 2
–
8
for an example). When using
the application kit, the calibration can be done in three
steps:
Step 1: Input of the registers which need not be
adjusted individually
The magnetic circuit, the magnetic material with its
temperature characteristics, the filter frequency, and
low and high clamping voltage are given for this appli-
cation.
Therefore, the values of the following registers should
be identical for all sensors of the customer application.
–
FILTER
(according to the maximum signal frequency)
–
RANGE
(according to the maximum magnetic field at the
sensor position)
–
TC and TCSQ
(depends on the material of the magnet and the
other temperature dependencies of the application)
–
CLAMP-LOW and CLAMP-HIGH
(according to the application requirements)
Write the appropriate settings into the
HAL 800
regis-
ters.
After writing, the information is stored in an internal
RAM and not in the EEPROM. It is valid until switching
off the supply voltage. If the values should be perma-
nently stored in the EEPROM, the
“
STORE
”
command
must be used before switching off the supply voltage.
Step 2: Calculation of V
OQ
and Sensitivity
The calibration points 1 and 2 can be set inside the
specified range. The corresponding values for V
OUT1
and V
OUT2
result from the application requirements.
For highest accuracy of the sensor, calibration points
near the minimum and maximum input signal are rec-
ommended. The difference of the output voltage
between calibration point 1 and calibration point 2
should be more than 3.5 V.
Set the system to calibration point 1 and read the reg-
ister ADC-READOUT. The result is the value ADC-
READOUT1.
Now, set the system to calibration point 2, read the
register ADC-READOUT again, and get the value
ADC-READOUT2.
With these values and the target values V
OUT1
and
V
OUT2
, for the calibration points 1 and 2, respectively,
the values for Sensitivity and V
OQ
are calculated as:
This calculation has to be done individually for each
sensor.
Now, write the calculated values for Sensitivity and
V
OQ
for adjusting the sensor.
Use the
“
STORE
”
command for permanently storing
the EEPROM registers. The sensor is now calibrated
for the customer application. However, the program-
ming can be changed again and again if necessary.
Step 3: Locking the Sensor
The last step is activating the LOCK function with the
“
LOCK
”
command. The sensor is now locked and does
not respond to any programming or reading com-
mands.
Warning:
This register cannot be reset!
Low clamping voltage
≤
V
OUT1,2
≤
High clamping voltage
V
OUT1
V
OUT2
ADC-READOUT1
ADC-READOUT2
Sensitivity =
V
DD
2048
*
ADC-READOUT1 * Sensitivity * V
DD
2048
V
OQ
= V
OUT1