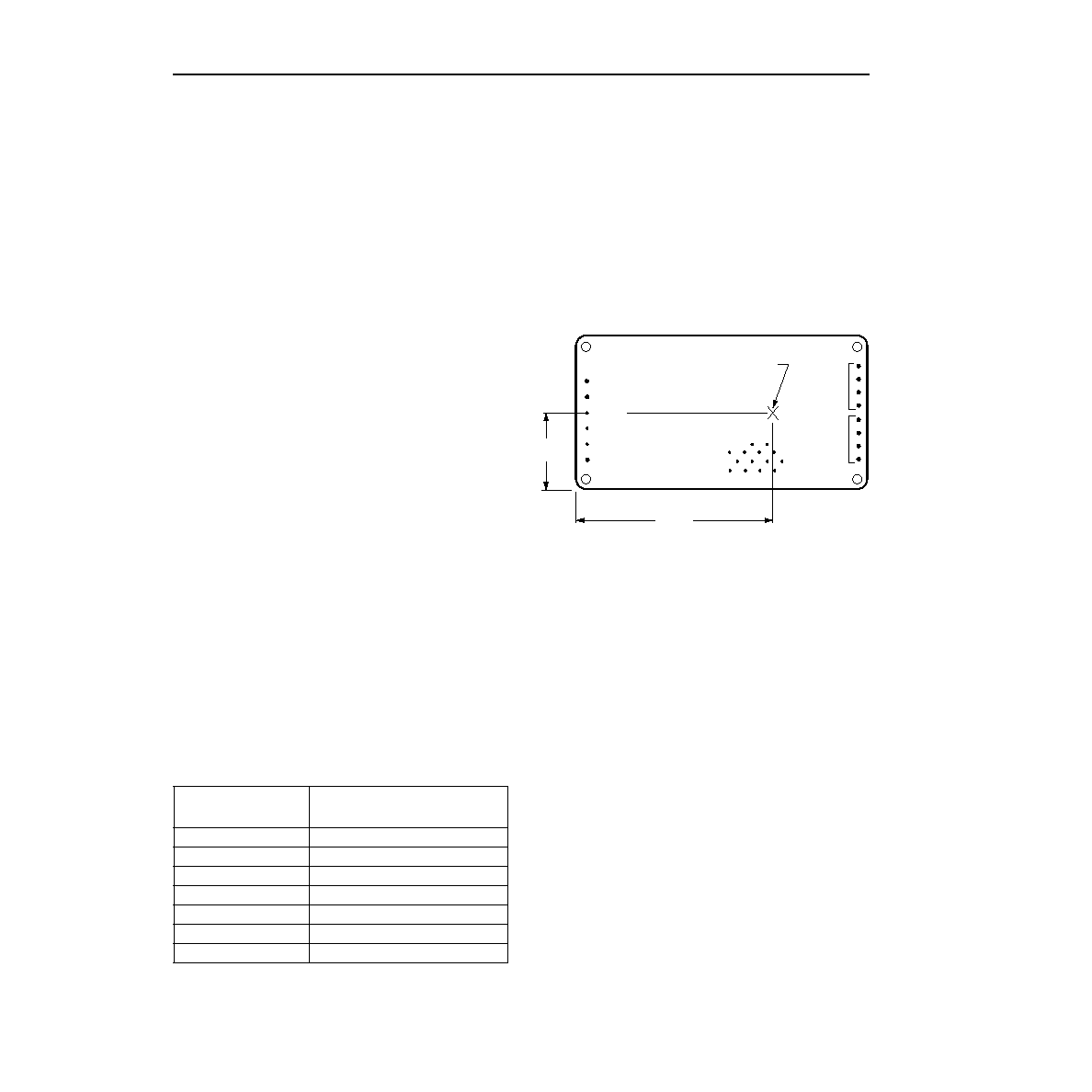
18
Tyco Electronics Corp.
Advance Data Sheet
March 2000
36 to 75 Vdc Input, 3.6, 3.3, 2.5, 2.0, or 1.8 Vdc Output; 180 W to 330 W
FW330 Power Modules: dc-dc Converters;
Feature Descriptions (continued)
Thermal Warning Signal
The thermal warning (THERM) pin is a secondary-ref-
erenced, open-collector output that shorts to
SENSE(–) a few degrees before the module goes into
thermal shutdown.
When the module temperature cools, the thermal warn-
ing pin will open, but the unit will remain latched off until
the input power or the primary or secondary referenced
remote on/off is recycled for 1.0 second.
Temperature Monitor
As an option a temperature monitor signal can be pro-
vided instead of the thermal warning signal (using the
same pin). The temperature monitor signal provides a
dc voltage proportional to the temperature of the mod-
ule as indicated in the Feature Specications table. For
example, on the FW330F1-T at 100 °C, the voltage on
the THERM pin would be 1.5 V. The temperature moni-
tor signal is referenced to the SENSE(–) pin on the
secondary and is supplied from a source impedance of
approximately 200 k
. It is recommended that the
THERM pin be left open when not in use, although no
damage will result if the THERM pin is shorted to sec-
ondary ground.
Module ID
The module ID signal allows the user to electronically
identify the module part number. This feature is useful
during customer factory assembly, before power is
applied, to ensure that the correct module is inserted. A
resistor placed between the Mod ID pin and SENSE(–)
pin has a resistance that correlates to the module part
number, as indicated in the following table:
Thermal Considerations
Introduction
The power modules operate in a variety of thermal
environments; however, sufcient cooling should be
provided to help ensure reliable operation of the unit.
Heat-dissipating components inside the unit are ther-
mally coupled to the case. Heat is removed by conduc-
tion, convection, and radiation to the surrounding
environment. Proper cooling can be veried by mea-
suring the case temperature. Peak temperature occurs
8-2823 (F)
Note: Top view, measurements shown in millimeters and (inches).
Pin locations are for reference only.
Figure 29. Case Temperature Measurement
Location
The temperature at this location should not exceed
100 °C. The maximum continuous case temperature
should be limited to a lower value for higher reliability.
The output power of the module should not exceed the
rated power for the module as listed in the Ordering
Information table.
Heat Transfer Without Heat Sinks
Derating curves for forced-air cooling without a heat
sink are shown in Figures
30 and
31. These curves can
be used to determine the appropriate airow for a given
set of operating conditions. For example, if the unit with
airow parallel to its longest side (longitudinal orienta-
tion) can dissipate 30 W of heat, the correct airow in a
40 °C environment is 1 m/s (200 ft./min.).
Module Part
Number
Mod ID Resistance
FW330S3R671-56
100 k
FW330F1
20.5 k
FW330F1-T
10 k
FW330F1-33T
5.11
FW330G71-56T
348 k
FW330D1
2490
FW330Y1-33T
681
CASE
SYNC IN
VI(–)
VI(+)
VO(–)
SYNC OUT
MEASURE CASE
TEMPERATURE HERE
ON/OFF
30.5
(1.20)
87.6
(3.45)
VO(+)