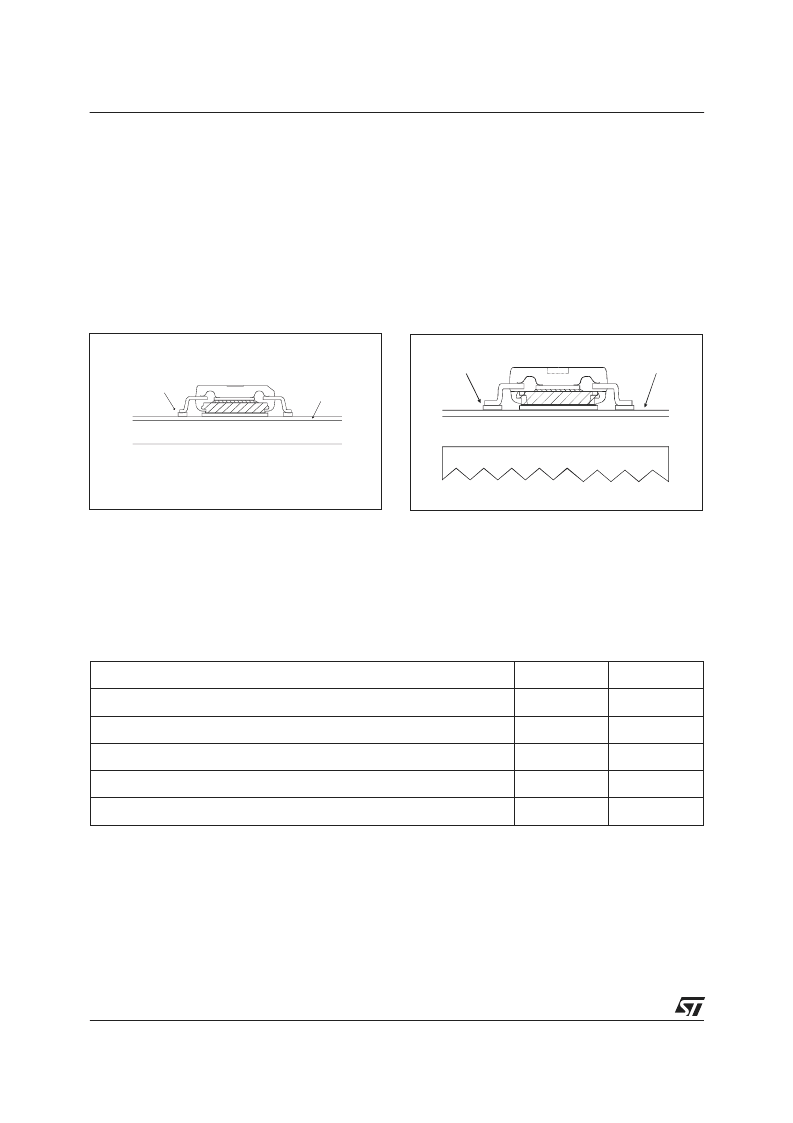
CLP270M
22/24
PowerSo-10 package mounted on
R
th
(j-a)
P Diss (*)
1.FR4 using the recommended pad-layout
50 °C/W
1.5 W
2.FR4 with heatsink on board (6cm
2
)
35 °C/W
2.0 W
3.FR4 with copper-filled through holes and external heatsink applied
12 °C/W
5.8 W
4. IMS floating in air (40 cm
2
)
8 °C/W
8.8 W
5. IMS with external heatsink applied
3.5 °C/W
20 W
(*) Based on a delta T of 70 °C junction to air.
TABLE 7 : THERMAL IMPEDANCE VERSUS SUBSTRATE
A new technology available today is IMS - an
Insulated Metallic Substrate. This offers greatly
enhanced thermal characteristics for surface
mount components. IMS is a substrate consisting
of three different layers, (I) the base material which
is available as an aluminium or a copper plate, (II)
a thermal conductive dielectrical layer and (III) a
copper foil, which can be etched as a circuit layer.
Using this material a thermal resistance of 8°C/W
with 40 cm
2
of board floating in air is achievable
(see fig. 39). If even higher power is to be
dissipated an external heatsink could be applied
which leads to an R
th
(j-a) of 3.5°C/W (see Fig. 40),
assuming that R
th
(heatsink-air) is equal to R
th
(junction-heatsink). This is commonly applied in
practice,
leading
to
dimensions. Often power devices are defined by
considering the maximum junction temperature of
the device. In practice , however, this is far from
being exploited. A summary of various power
management capabilities is made in table 1 based
on a reasonable delta T of 70°C junction to air.
reasonable
heatsink
Fig 39 :
Mounting on metal backed board
Fig 40 :
Mounting on metal backed board with an
external heatsink applied
FR4 board
Copper foil
Aluminium
heatsink
Copper foil
Insulation
Aluminium
The PowerSO-10 concept also represents an
attractive
alternative
to
PowerSO-10 offers devices fully tested at low and
high temperature. Mounting is simple - only
conventional SMT is required - enabling the users
to get rid of bond wire problems and the problem to
C.O.B.
techniques.
control the high temperature soft soldering as well.
An optimized thermal management is guaranteed
through PowerSO-10 as the power chips must in
any case be mounted on heat spreaders before
being mounted onto the substrate.