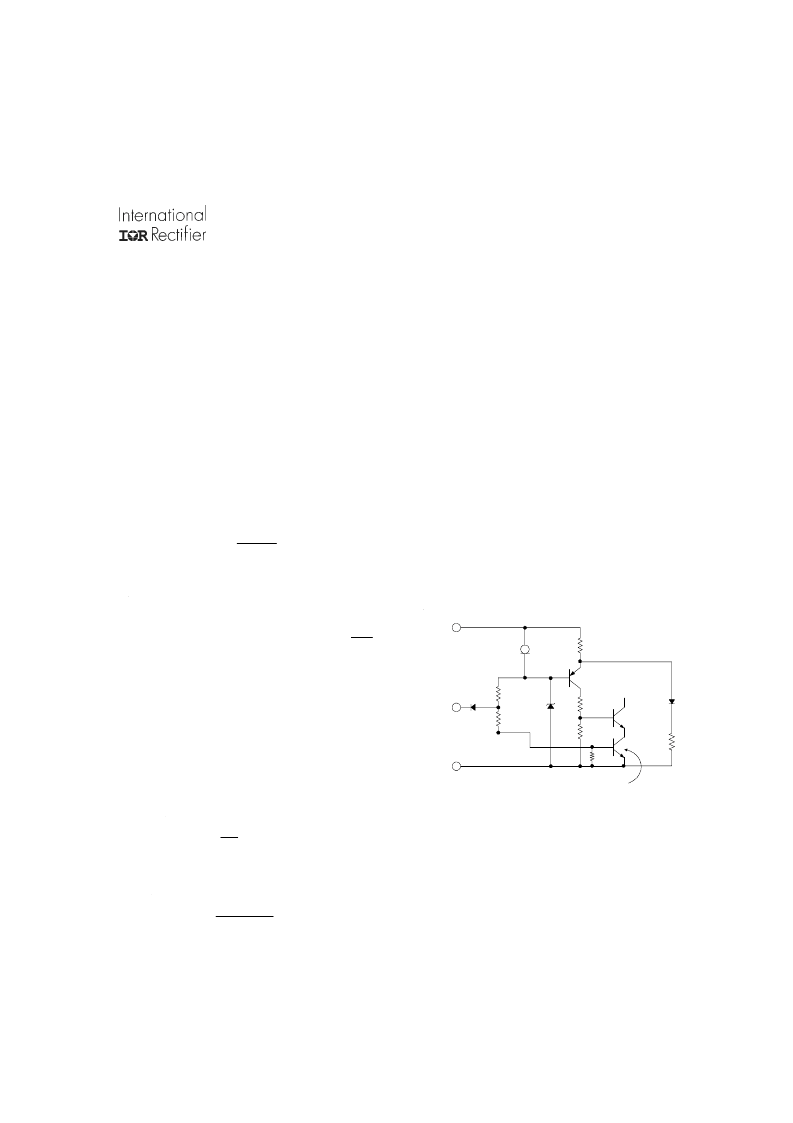
www.irf.com
7
ART28XXT Series
Effectiveness of this heat transfer is dependent on the
intimacy of the baseplate-heatsink interface. It is therefore
suggested that a heat transferring medium possessing
good thermal conductivity is inserted between the
baseplate and heatsink. A material utilized at the factory
during testing and burn-in processes is sold under the
trade name of Sil-Pad
4001. This particular product is an
insulator but electrically conductive versions are also
available. Use of these materials assures optimum surface
contact with the heat dissipater by compensating for minor
surface variations. While other available types of heat
conducting materials and thermal compounds provide
similar effectiveness, these alternatives are often less
convenient and are frequently messy to use.
A conservative aid to estimating the total heat sink surface
area (A
HEAT SINK
) required to set the maximum case
temperature rise (
T) above ambient temperature is given
by the following expression:
A
HEAT SINK
≈
T
P
80
594
.
0 85
.
1 43
.
T
P
P
Eff
OUT
=
=
=
Case temperature rise above ambient
Device dissipation in Watts
1
1
where
As an example, assume that it is desired to maintain the
case temperature of an ART2815T at +65°C or less while
operating in an open area whose ambient temperature
does not exceed +35°C; then
T = 65 - 35 = 35°C
From the Specification Table, the worst case full load
efficiency for this device is 80%; therefore the maximum
power dissipation at full load is given by
(
)
P
=
=
=
30
1
80
.
1
30
025
.
75
. W
and the required heat sink area is
A
=
35
80 7.5
in
HEAT SINK
0.85
=
143
.
2
594
.
318
.
1Sil-Pad is a registered Trade Mark of Bergquist, Minneapolis, MN
Thus, a total heat sink surface area (including fins, if any)
of approximately 32 in2 in this example, would limit case
rise to 35°C above ambient. A flat aluminum plate, 0.25"
thick and of approximate dimension 4" by 4" (16 in2 per
side) would suffice for this application in a still air
environment. Note that to meet the criteria, both sides of
the plate require unrestricted exposure to the ambient air.
Inhibiting Converter Output
As an alternative to application and removal of the DC
voltage to the input, the user can control the converter
output by providing an input referenced, TTL compatible,
logic signal to the enable pin 3. This port is internally pulled
“high” so that when not used, an open connection on the
pin permits normal converter operation. When inhibited
outputs are desired, a logical “l(fā)ow” on this port will shut the
converter down. An open collector device capable of
sinking at least 100 μA connected to enable pin 3 will work
well in this application.
Figure II. Enable Input Equivalent Circuit
A benefit of utilization of the enable input is that following
initial charge of the input capacitor, subsequent turn-on
commands will induce no uncontrolled current inrush.
118K
2N2907A
150K
Enable
Input
Input
Return
150K
2N2222A
2N2222A
V
in
64K
186K
150K
5.6 V
Converter inhibit is initiated when
this transistor is turned off
65K
CR2