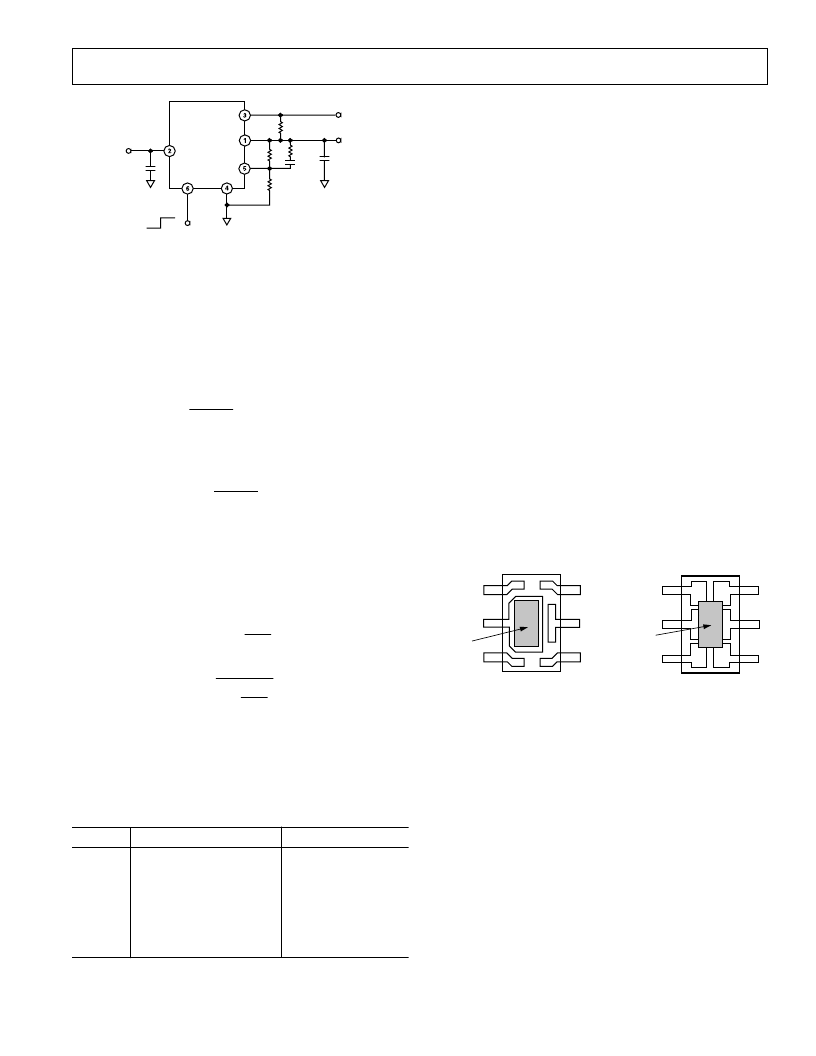
REV. 0
ADP3331
–7–
V
OUT
V
IN
+
ADP3331
FB
OUT
ERR
ON
OFF
SD
GND
IN
C2
0.47
m
F
C1
0.47
m
F
+
E
OUT
R3
R1
R2
R
NR
C
NR
Figure 21. Noise Reduction Circuit
Output Voltage
The ADP3331 has an adjustable output voltage that can be set
by an external resistor divider. The output voltage will be di-
vided by R1 and R2, and then fed back to the FB pin. Refer to
Figure 21.
In order to have the lowest possible sensitivity of the output
voltage to temperature variations, it is important that the paral-
lel resistance of R1 and R2 is always 230 k
:
R
R
R
R
k
1
1
2
2
230
×
+
=
Also, for the best accuracy over temperature the feedback volt-
age should set for 1.204 V:
V
R
+
R
R
V
OUT
FB
2
1
2
=
where
V
OUT
is the desired output voltage and
V
FB
is the “virtual
bandgap” voltage. Note that V
FB
does not actually appear at the
FB pin due to loading by the internal PTAT current.
Combining the above equations and solving for R1 and R2 gives
the following formulas:
R
V
V
k
R
V
V
k
OUT
FB
FB
OUT
1
230
2
230
1
=
=
The output voltage can be adjusted to any voltage from 1.5 V to
10 V. For example, the Feedback Resistor Selection Table shows
some representative feedback resistor values for output voltages
in the specified range.
Table I. Feedback Resistor Selection
V
OUT
R1 (1% Resistor)
243 k
340 k
422 k
511 k
634 k
953 k
1.00 M
R2 (1% Resistor)
1.00 M
698 k
511 k
412 k
365 k
301 k
154 k
1.5 V
1.8 V
2.2 V
2.7 V
3.3 V
5 V
9 V
Output voltages above 5 V and below 1.6 V will require non-
standard resistor values or adding an additional resistor to the
divider network to achieve the best performance. Using stan-
dard values as shown in Table I will sacrifice some temperature
stability.
Output Current Limit
The ADP3331 is short circuit protected by limiting the pass
transistor’s base drive current. The maximum output current is
limited to about 300 mA.
Thermal Overload Protection
The ADP3331 is protected against damage due to excessive
power dissipation by its thermal overload protection circuit.
Thermal protection limits the die temperature to a maximum of
+165
°
C. Under extreme conditions (i.e., high ambient tempera-
ture and power dissipation) where the die temperature starts to
rise above +165
°
C, the output current will be reduced until the
die temperature has dropped to a safe level.
Current and thermal limit protections are intended to protect
the device against accidental overload conditions. For normal
operation, the device’s power dissipation should be externally
limited so that the junction temperature will not exceed 125
°
C.
Chip-on-Lead
The ADP3331 uses a patented Chip-on-Lead package design to
ensure the best thermal performance in an SOT-23 footprint.
The standard SOT-23 depends on the majority of the heat to
flow out of the ground pin. The Chip-on-Lead package uses an
electrically isolated die attach, which allows all the pins to
contribute to heat conduction. This technique reduces the ther-
mal resistance to 190
°
C/W on a 2-layer board as compared to
>230
°
C/W for a standard SOT-23 lead frame. Figure 22 shows
the difference between the standard SOT-23 and the Chip-on-
Lead lead frames.
SILICON DIE
WITH
ELECTRICALLY
ISOLATED
DIE ATTACH
SILICON
DIE
NORMAL SOT-23-6 PACKAGE
THERMALLY ENHANCED
CHIP-ON-LEAD PACKAGE
Figure 22.Chip-on-Lead Package
Calculating Junction Temperature
Device power dissipation is calculated as follows:
P
D
= (
V
IN
–
V
OUT
)
I
LOAD
+ (
V
IN
)
I
GND
Where
I
LOAD
and
I
GND
are load current and ground current,
V
IN
and
V
OUT
are the input and output voltages respectively.
Assuming the worst case operating conditions are I
LOAD
=
200 mA, I
GND
= 4 mA, V
IN
= 4.2 V and V
OUT
= 3.0 V, the
device power dissipation is:
P
D
= (4.2
V
– 3.0
V
) 200
mA
+ (4.2
V
) 4
mA
= 257
mW
The proprietary package used on the ADP3331 has a thermal
resistance of 165
°
C/W when placed on a 4-layer board, and
190
°
C/W when placed on a 2-layer board. This allows the ambi-
ent temperature to be significantly higher for a given power
dissipation than with a standard package. Assuming a 4-layer
board, the junction temperature rise above ambient will be
approximately equal to:
T
J
A
= 0.257
W
×
165
°
C/W
= 42.4
°
C