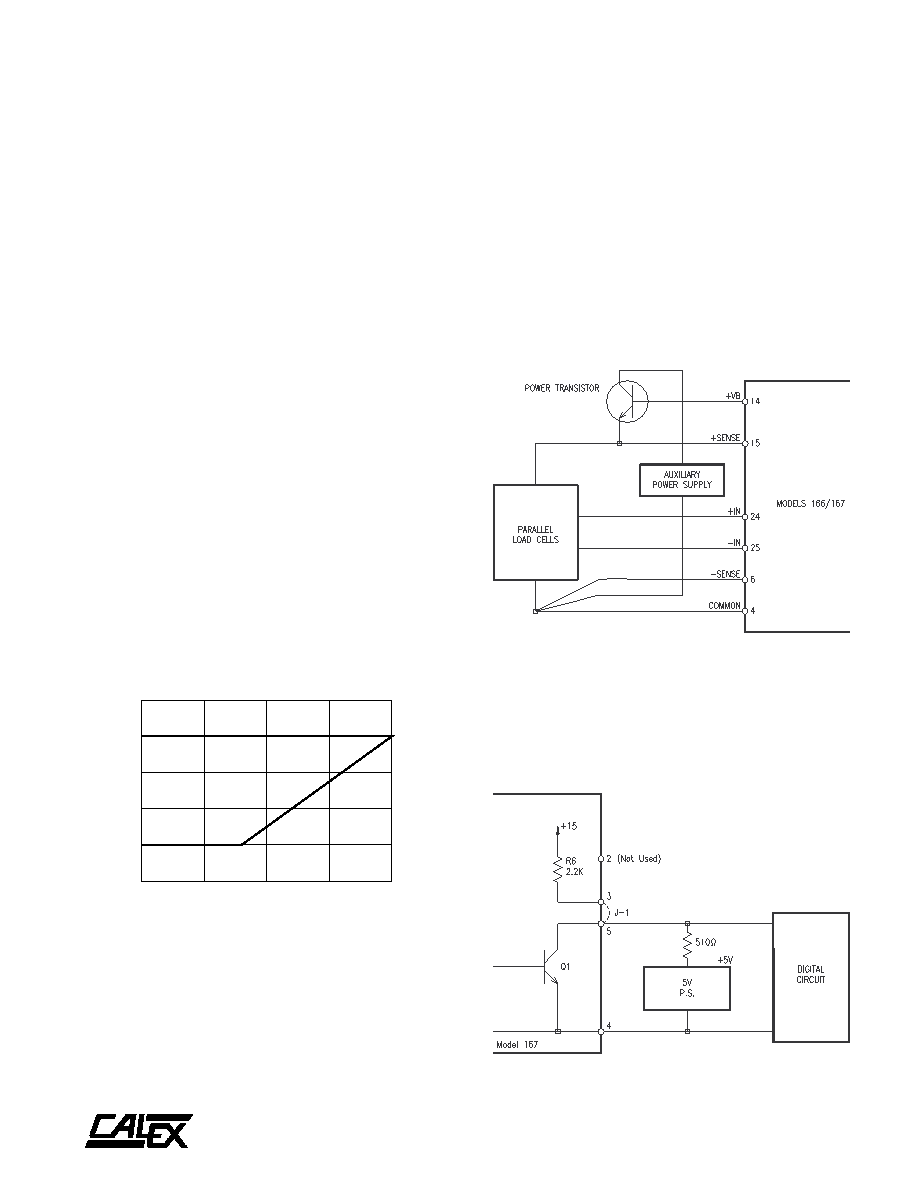
A
4
CALEX
FaxFACTS:
315
1997
Models 166 and 167 Bridgesensors
http://www.calex.com
2401 Stanwell Drive
Concord, CA 94520-4841
(510) 687-4411 Fax (510) 687-3333
Input Offset
The external adjustment circuit shown in Figures 1 and 2 will
allow the amplifier input offset to be changed over a range of
approximately ±2 mV referred to the input. The primary
purpose is to adjust the internal amplifier offset to zero; it is
not intended to compensate for an unbalanced load cell
bridge. When the Model 166 or 167 is purchased on an
MK166/7 mounting kit, the offset potentiometer is factory set
for minimum offset. If it is necessary to adjust input offset, first
short the two inputs to common (pins F, H and J) and then
adjust the input offset potentiometer until the amplifier output
voltage is minimum (zero volts).
If it is necessary to use this adjustment to compensate for an
unbalanced load cell bridge, it can be done, but it should be
remembered that in so doing, the amplifier offset drift with
temperature will be degraded.
Output Offset
The output of the instrumentation amplifier can be intentionally
offset from zero by applying a voltage to pin 20 of the module.
It should be noted that the offset introduced by this means is
not amplified by the gain, while input offset is. The output can
be offset to allow for tare weight compensation. For example,
if the container weighs 50 pounds when using a load cell of
1000 pound range, the output of the amplifier may be offset
to +0.5 Volt. The weight of the container will then cause the
amplifier output to go to zero volts and as load is added the
amplifier output will increase in the negative direction causing
the V/F converter to operate. In order to minimize the effect
of degrading the common mode rejection ratio, the voltage
applied to pin 20 should come from a low impedance source
such as the output of an operational amplifier.
MODELS 166 & 167
BRIDGE SUPPLY VOLTAGE Vs OUTPUT CURRENT
0
25
50
75
100
OUTPUT CURRENT (mA)
2
4
6
8
10
12
BRIDGE
SUPPLY
VOLTAGE
(VOLTS)
↑
←
SAFE
OPERATING
AREA
→
↓
FIGURE 3. Bridge Output Current
with a mounting kit, MK166/7, a multiturn potentiometer is
provided for this purpose on the MK166/7. It is factory set for
a scale factor of 1 kHz or 10 kHz per volt. The temperature
coefficient of the mounting kit pot is ±100 ppm/°C. If better
temperature stability is required, the scale factor pot should
be replaced with a precision, temperature stable resistor.
Scaling adjustment is done by changing the amplifier gain or
by the V/F scale factor adjustment. These two adjustments
allow the user to treat the amplifier and the V/F converter
independently if desired. In Figure 2, the amplifier gain would
be set so that -10 Volts output would represent full scale, 1000
pounds for example. The V/F scale factor would be set for full
scale output of 10 kHz or 100 kHz. If a 0.1 second time base
were selected for the Model 166 and 0.01 second for the
Model 167 then a load of 999 pounds would be displayed as
999.
FIGURE 4. Using an External Current Booster
V/F Converter Output
Model 166 provides for auxiliary output or optically isolated
output. The auxiliary output is taken between the collector of
Q
1 and common. Q1 can sink 50 mA. When used as a source,
the auxiliary output can supply a 10 volt pulse into a 3k load
resistor.
V/F Scale Factor Adjust
To set the V/F scale factor, connect an external resistance
from pin 1 of the module to common. The value of the
resistance is approximately 3 kohms. Calibration is performed
by applying -10.000Volts to pin 31 and then adjusting the
external resistor until the output frequency is 10.000 kHz or
100.00kHz as appropriate. When the Model 166/7 is purchased
FIGURE 5. Model 167 Output Circuit
To drive CMOS, eliminate the 5V P.S
and the 510
resistor and install J-1.